Mobile Elevating Work Platforms
Need to speak to an engineer? Contact our team today.
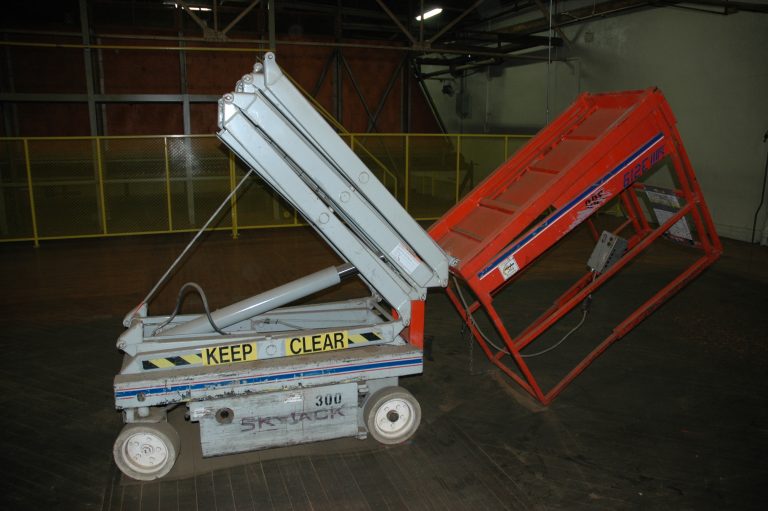
Gary E. Kilpatrick, PE, DFE is a certified operator and trainer for operating and inspecting Mobile Elevating Work Platforms (MEWPs). These machines use to be referred to as Aerial Work Platforms. The OSHA safety regulations and the ANSI/SAIA standards have changed drastically. These new OSHA regulations and standards went into effect on March 1st 2020. If a company who uses these machines is not compliant, they can be fined and cited by OSHA. Each machine must have three manuals stored on it namely (1) the Operators Manual; (2) the Manual of Responsibilities and (3) the Aerial Platform Safety Manual. Every employee who is certified to operate a MEWP must read and understand these manuals before he or she operates these machines. Gary travels and performs forensic engineering investigations and inspections on MEWPs for law firms and insurance companies nationwide. Gary performs the following forensic engineering services:
- MEWP forensic engineering investigations, inspections and reconstruction
- MEWP maintenance and standards of care analyses
- MEWP forensic engineering performance testing
- MEWP operations
- MEWP forensic engineering component and product defect and failure analyses
- MEWP safety requirements
- MEWP personal fall protection equipment PFPE inspection
- MEWP determine proper machine choice for the job at hand
- MEWP determine if the machine is designed for indoor or outdoor operation
- MEWP hazard analyses
- MEWP training determination and analyses
- MEWP Safe Use Plan review and analyses
- MEWP Rescue Plan review and analyses
- MEWP system document reviews
- The Operators Manual, Aerial Safety Manual, and the Manual of Responsibilities must be stored on the machine on the base/ground unit and/or in the operator’s platform
Mobile Elevating Work Platforms (MEWPs) is the new term describing the old term used in the older ANSI standards of Aerial Work Platforms (AWPs). The new laws and standards went into effect on March 1st 2020.
MEWP classifications were created for a combination of two key descriptions below:
The MEWP “Group” determines where the personnel platform is located in reference to the lifting machine’s tipping line. There are two Groups “A” and “B”.
The MEWP “Type” refers to the lifting machine’s ability to travel relative to the personnel platform’s position.
“Group A” are the lifting machines that lift personnel straight up over the machine’s base such as the Scissor Lift or a Stationary Vertical Lift.
“Group B” are the articulated or telescopic boom personnel lifting machines.
“Type 1” personnel lifting machines are stationary, manually propelled or trailer mounted and traveling is allowed with the MEWP in its stowed position. Examples of these MEWPs would be Type 1 Group A 1A Stationary Vertical MEWP; Type 1 Group B 1B Stationary Boom MEWP.
“Type 2” personnel lifting machines traveling with the personnel platform above the base is controlled from the ground using the control panel located on the machine base.
“Type 3” personnel lifting machines are self-propelled and can have the articulated or telescoping booms and traveling with the personnel platform elevated above the base is controlled from the control panel on the personnel platform. Examples of these MEWPs would be Type 3 Group A 3A Platform Controlled Mobile Vertical MEWP; Type 3 Group B 3B Platform Controlled Mobile Boom MEWP.
ANSI Standards that apply to MEWPs are ANSI/SAIA A92 and the ANSI Manual of Responsibility. Canada has a national standard CSA B354.
The MEWP’s Operator’s Manual and the Manual of Responsibility must be kept on the personnel platform in a water-tight compartment usually located down below the control panel.
All operators as well as other occupants in the personnel platform must have a basic level of knowledge of work safety on a MEWP. This includes:
- Fall Protection and anchor locations inside the personnel platform.
- Factors on how bodily actions and movements can affect stability.
- Safe use of accessories.
- Any site work procedures MEWP operators and occupants must follow related to the operation of the MEWP.
- Hazards associated with the job and their avoidance.
- MEWP manufactures warnings and instructions listed in the operator’s manual, The Manual of Responsibilities, and posted on warning labels located on the machine.
- At least one of the MEWP occupants must be trained with the knowledge to operate the personnel platform controls in an emergency when the operator cannot perform this himself/herself.
Hazards Associated With MEWPs:
- Tip-Over Hazards
- Fall Hazards
- Collision Hazards
- Electrocution Hazards
- Trapping and Crushing
Personal Fall Protection Equipment (PFPE): Any person who will be utilizing a MEWP such as an operator and occupant must utilize PFPE. The selection of PFPE is very important. The length of the PFPE must be shorter than the fall distance by at least 3 feet. PFPE must be replaced every five years even if it looks like it is in excellent condition. Materials making up the PFPE can degrade over time and especially when exposed to direct sunlight. PFPE must be inspected and these inspections must be documented. If the PFPE has been used in a fall, then the entire harness and mechanisms must be discarded. PFPE is an OSHA requirement per OSHA 29 CFR 1926.453(b)(2)(v); OSHA 29 CFR 1926.502; OSHA 29 CFR 1910.66 and Standards ANSI A92.2; ANSI A92.5; ANSI Z359 and ANSI A10.32. Also refer to the Miller Fall Protection Safety Guide.
Inspections: These machines must be inspected per the manufacturer’s instructions detailed in the Operator’s Manual by each user each day no matter how many users utilize the machine each day. These machines must also be inspected every three months or every 150 hours of use whichever comes first and also annually by a qualified service technician.
Training: Both the supervisors and operators must be trained and certified to operate and inspect these machines. All training must be documented. Re-Training may be required depending on the following situation:
- Expired operator’s training period.
- Operator’s performance has deteriorated.
- Near miss.
- Operator was involved in an accident.
- Operator has gone for an extended period of time without operating a MEWP.
- The operator has been assigned to a different MEWP with different technology.
Safe Use Program: The Owner/User must develop a Safe Use Program that includes but is not limited to the following:
- Risk Assessment to identify all hazards, develop control plans and communications for every employee who operates MEWPs.
- Selection of suitable MEWPs; MEWP Range of Motion and Associated Equipment.
- Access, preparation and maintenance of the work site which will include an assessment of the Support Surface which must be adequate to support the weight of the MEWP, its occupants and accessories.
- MEWP maintenance including all inspections and repairs as required.
- Inform the operator of site requirements and warnings to provide a means for protection against identified hazards in the area where the MEWP will be utilized.
- Must have a trained and qualified supervisor to monitor the activities of the operator to ensure compliance with the ANSI/SAIS A92 standard.
- Prevention of unauthorized use of a MEWP.
- Safety of personnel not involved with the operation of the MEWP such as pedestrians.
Rescue Plan: This plan will be performed in case of a machine breakdown, platform entanglement or fall. The Rescue Plan must be in writing and become part of the companies training manual. All users must receive this training that explains the procedures in case of an entanglement or fall. This plan must limit the time a properly retrained user hangs suspended below the MEWP. A Rescue Plan can include:
- Self-Rescue by the user utilizing the appropriate equipment.
- Assisted Rescue by others that witness the event on the work site.
- Technical Rescue by the fire department and/or EMS.